TESTING STAR TREK REPLICATORS
March 9, 2017
As a Star Wars fan, writing stuff about “Trek” is a bit awkward. Nonetheless, the replicator is a fascinating machine. The replicator made its first real appearance in The Next Generation series of Star Trek already in 1987. In older Star Trek series, there were hints towards a replicator but only as a bio-matter or protein re-sequencer. In that sense, it only started with replicating food.
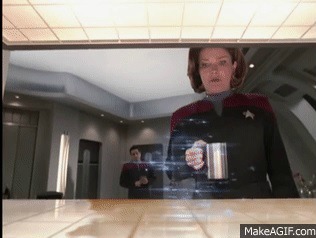
Now let’s jump to current developments with 3D printing or additive manufacturing. This technology is now letting us have first versions of real replicators. My background is firmly rooted in testing, so testing such a machine is on my wish list. Testing a 3D printer may not directly be my first challenge. The commercial 3D printers are widely available, hopefully, they are tested well. Looking at the stuff that comes out of the printer sparked my interest. Material properties of 3D printed structures like strength or temperature distribution are different compared to other manufacturing methods.
Last week a colleague presented me with the top 10 challenges and the top 10 principles regarding 3D printing. He also wrote a nice blog about this on LinkedIn. Let’s look at these lists:
10 Principles of 3D printing (BigThink):
Principle one: Manufacturing complexity is free
Principle two: Variety is free
Principle three: No assembly required
Principle four: Zero lead time
Principle five: Unlimited design space
Principle six: Zero skill manufacturing
Principle seven: Compact, portable manufacturing
Principle eight: Less waste by-product
Principle nine: Infinite shades of materials
Principle ten: Precise physical replication
10 Challenges of 3D printing the Media doesn’t tell you about (Posted by THEFULLAPPLE)
- It’s damn difficult to get right
- Scott Crump’s patent delayed progress by 20 years
- The 3D Printing market is two faced
- They’re still pretty expensive
- You need some amount of technical know how
- A watched model never prints…
- Quality, not quantity – or neither?
- Life support
- Material world
- A perfect end to a non-perfect print
Considering these lists, I see huge possibilities for 3D printing with a considerable way to go where technology is concerned. The ideas and potential savings in money, speed (time to market) and tech are very promising. The simple and quick output of a replicator is still some time away. Research-wise, all technology is there. To get this into commercial shape or eventually in our homes is the step to look at.
Now we know we can print everything (in the near future at least!). The future possibilities are endless. Looking at future scenarios for 3D printing we can combine those to see that replicators can help repairing human bodies. Let’s combine future scenario’s like the self-healing vehicle with printing complex organs: Not only prosthetics but any damage to the body from a simple cut to fractures or sick organs can be automatically fixed!
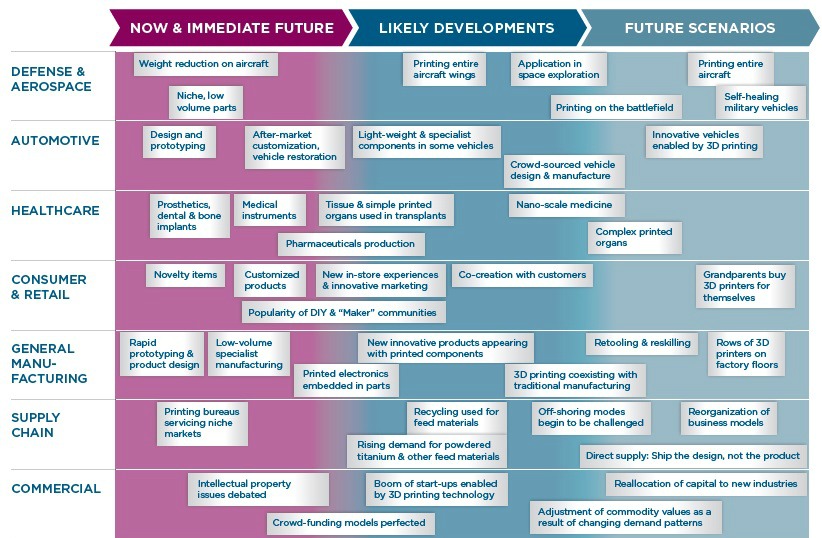
Ok, this is all considering the future. Let’s take a moment to see what is happening now and what is needed to make the replicator become a reality. Current 3D printers print what we tell them to. The result is hopefully something resembling what you have designed. What we do not know is how good the printed result is. The strength, temperature distribution and stress points, for example, may differ from what we would expect with conventional manufacturing methods. Before 3D printing is going to make a flight, we must know the behavior of these properties when 3D printing.
Testing 3D printed structures is an activity not to be underestimated. Of course, testing after printing can be done. It takes considerable time to print, therefore if we know more about 3D printed material behavior before it is printed, this is very helpful. A 3D print goes through different phases (from idea to design to actual (multiple versions of) prints). Testing in each phase helps to get the product (first time) right and at a quality level that is expected. Setting up testing for additive manufacturing can be an extension for TMap. The base TMap gives us can be reused and the phases for 3D printing can be added.
By putting 3D print test activities to each phase, a rudimentary additive manufacturing test strategy is here:
- Design and test your design, review for testability
- Simulate design for printing and test if the design can be made
- Simulate printed product properties (FEA on temperature distribution, stress)
- Print! (Test layers during printing, fill any gaps found)
- Physical test the printed product on product properties (compare with other production methods)

Testing the star trek replicator is not about testing the machine itself but about testing its output. Let’s finish off with two things that I think are worth thinking about where 3D print test activities are concerned:
- What kind of prints do we need to run through the replicator to test that the replicator replicates? Eventually, it should be possible to replicate a replicator.
- How do we make sure no flaws come into next generations of replicators? Almost like new populations where genes are given through and a tiny gene alteration is of massive impact to next generations (of prints in this case).
There are is great stuff going on in the world of additive manufacturing. With the Star Trek replicator well on its way, additive manufacturing testing is crucial!
Related posts